BAUSCHER
References
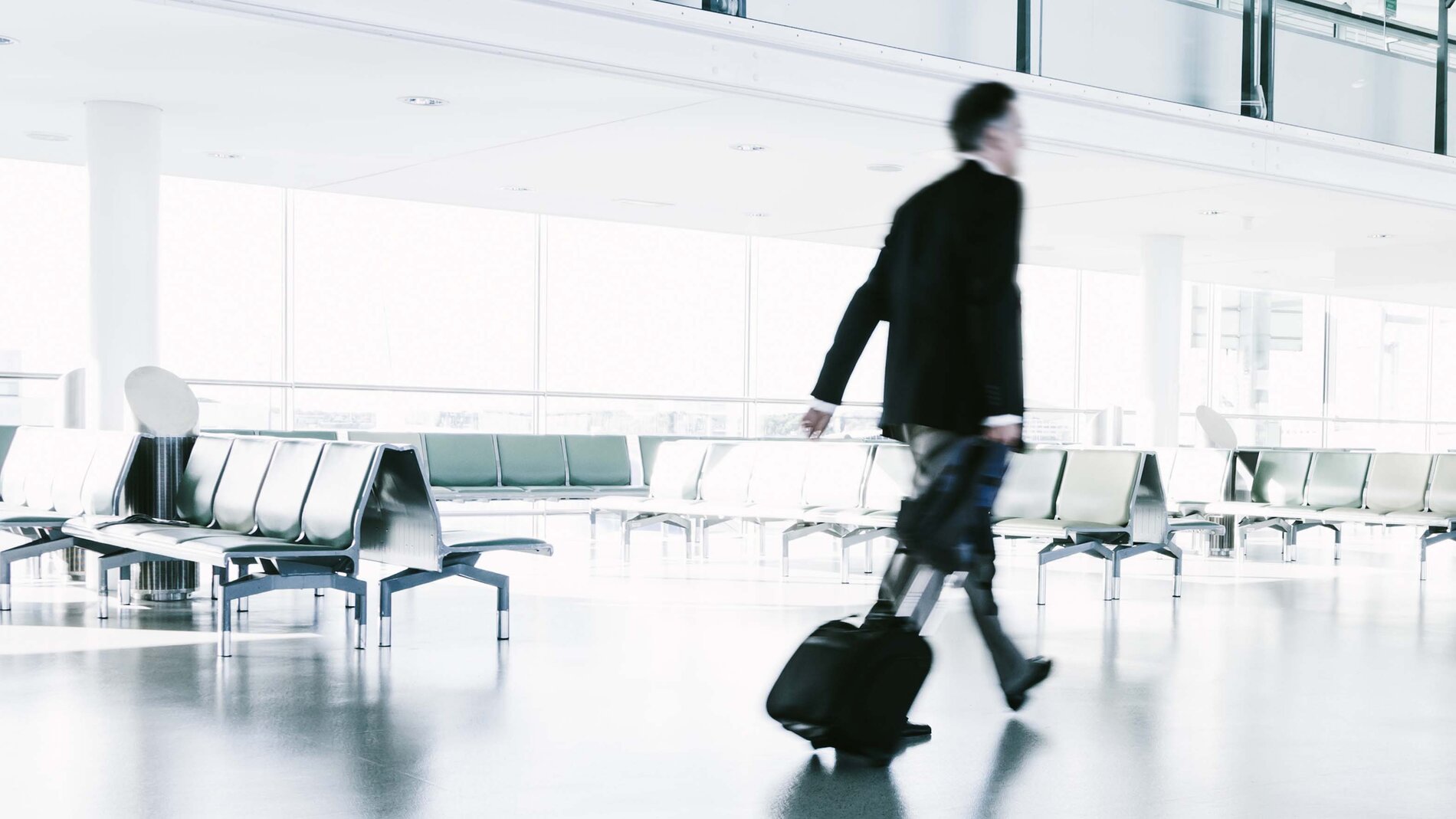

Restaurant & Hotel Schlossberg Thun
Living in a castle steeped in history, a unique view over the city and varied kitchen creations, staged on the finest porcelain from BAUSCHER: The newly opened Restaurant & Hotel Schlossberg Thun (Switzerland) promises its guests an unforgettable culinary experience. For their unique concept, the hosts Alexandra Bonazzi Hofschneider and Stefan Hofschneider rely on exceptional porcelain - the snacks and dishes are therefore presented on the new, highly elegant BAUSCHER collection PURITY.
Tradition and modernity stylishly combined
For BAUSCHER and its Swiss exclusive partner Berndorf Luzern, the project held some special challenges: "There were only three weeks between the decision in favor of Purity and the opening," says Beat Hämmerlin, who is responsible for the project in Berndorf Luzern's sales force. "That is already an extremely short time, especially since the collection was still completely new on the market at the time. Nevertheless, we managed to deliver all the porcelain items on time." As a result, 39 different items from the BAUSCHER PURITY collection are now in use at Restaurant & Hotel Schlossberg Thun - a total of around 4,200 porcelain pieces.

BAUSCHER is supplying BASF and Bosch with intelligent tableware
The largest chemical group in the world is counting on Pabis by BAUSCHER at two staff cafeterias at its location in Ludwigshafen. With the intelligent accounting system, the entire cash register process takes place automatically.
PABIS: Payment by intelligent solutions
Tableware, fitted with a chip that processes the payment – a vision for the future or reality? PABIS stands for Payment by intelligent solutions. Antenna spaces in which the name and price of a dish is stored are integrated into the food service counters. If you hold your plate with that particular dish over this space, the transponder in the bottom of the plate is “read” with the help of RFID technology. When the customer goes to the cash register, there is no longer a staff member sitting there because the transponder transmits the stored information electronically. The guest sees how much it costs on the POS display and makes a non-cash payment. This technology works quickly and effectively – this is particularly appealing to companies that are leading the way in digital networking. In March 2016, PABIS was installed in the first Bosch cafeteria.
Less Waiting Time, improved Scope for Financial Planning
“Optimized company catering is generally interesting for all larger companies. In addition, interest in Industry 4.0 is further driving demand for our intelligent porcelain. Reference customers such as BASF and Bosch, who are important players in the area, also do their part. BAUSCHER has assumed a pioneering role, and in collaboration with avus Services, is providing a complete solution that up to now has not otherwise been available”, says Nelson Mauricio, Director Executive Sales.

AIRFLOW at the Protestant Hospital Niederrhein
A strong network at four locations. The Evangelisches Klinikum Niederrhein in Duisburg-Nord has over 1.274 beds in the western Ruhr region with its 27 departments at four locations: two in Duisburg, one in Dinslaken, and one in Oberhausen.
The Protestant Hospital Niederrhein is a teaching hospital of Heinrich-Heine-Universität Düsseldorf. The network also includes two nursing facilities in Duisburg and Oberhausen. In light of the fact that all kitchens were “getting on” and would require huge investments for their restoration, it was decided to erect a central kitchen at the Duisburg-Nord location and supply all locations from there.
n order to ensure that the quality of the meals did not deteriorate over the distances traveled, it was necessary to do away with the “freshly made” principle. After various deliberations, inspections, and tests, the “cook & chill” production method was selected. In fall 2017 the new central kitchen commen-ced operations and the system was introduced successively at all locations.
Step by Step to the perfect System Solution
Based on the positive results obtained from use of the contact heating system from ELECTRO Calorique since 2004 and following tests and consideration of economic factors, the latest generation of this system was chosen. The tableware used had to be coordinated with the contact heating system, functional, stable, and, above all, space-saving and hence cost-effective. All meal components had to be arranged in a visually appealing way on the special partitioned Gastronorm tray and covered hygienically. For economic reasons, the existing tableware stackers had to be coordinated with and integrated into the new central kitchen.
Following a number of consultations, sample evaluations, and tests, a decision was made in favor of the latest special AIRFLOW collection and the special plates with plain bottom for the contact heating system. Thus, the longstanding close and successful cooperation could be continued. Coordination of the tableware with the existing tableware stackers and the integration and conversion of the tableware were achieved with the help of the Bauscher team in two steps during running operations. The focus was laid on ensuring a smooth workflow, especially in the dishwashing area, as well as on joint development of an organizational concept for storage of the cooled tableware.